This process carries a pair of parts, and then does spot welding in 3 locations per part. Until now, because it was done manually, more workers were needed to increase production to meet customer demand. In addition, since the project of high-mix low-volume production has been increasing in recent years, the welding process was automated using our
ROBO Cylinders this time. It cost $12,000 ($6,000 / unit × 2 units) to build the two units, but it was amortized over 7.5 months.
(Personnel Expenses was calculated at $10 / hour)
After changing to ROBO Cylinder
- Due to the manual labor, large differences had come out in production volume and quality depending on the workers. But with the result of the automation, since the parts stop at the same location repeatedly for welding, the quality is stable, and the defects became almost zero.
- Compared to the manual labor, cycle time is improved, and production has increased significantly.
- Since the worker was now only responsible for the placement and removal of the parts, and they can now handle the two units alone, the labor cost is now half.
Reduction in Cycle Time/Choco Tei - CT Effects
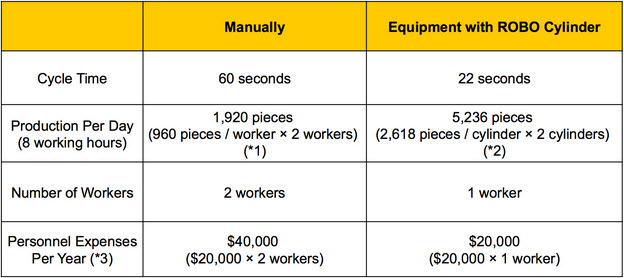
;
(*1) Production amount done manually per 1 worker: 8 hours per day /60 seconds = 480 pair = 960 pieces
(*2) Production amount with ROBO Cylinders per 1 unit: 8 hours per day /22 seconds = 1,309 pair = 2,618 pieces
(*3) Annual personnel expenses per 1 worker: ($10 per hour x 8 hours) x 250 days = $20,000
Want to Learn More About IAI?