-
- bimba
- Universal Robots
- dorner
- cobots
- industrial automation nj/ny
- Dorner Conveyors,
- The Knotts Co
- The Knotts Company
- UR
- manufacturing
- Robots
- PLC
- Unitronics
- automation
- humphrey products
- knotts company
- solutions
- HMI
- conveyors
- robotics
- aluminum extrusion
- aluminum extrusion in nj
- automation solutions
- engineered solutions
- air cylinder
- cost effective
- cost savings
- cobot
- collaborative robots
- t-slotted extrusion
- bimba solutions
- technology
- MiR
- Robotiq
- Humphrey
- IAI
- WAGO
- bimba pneumatic
- machine guard
- smartflex conveyors
- solution
- assembly
- collaborative robot
- cylinder
- electric cylinder
- motion control
- sanitary conveyor
- 2200 Series
- Products
- automation control
- conveyor
- core competencies
- grippers
- pharmaceuticals
- resource
- robot
- AquaPruf
- Asycube
- Asyril
- Cage Clamp
- Machine Guarding
- Mobile Robots
- Norgren
- OptoForce
- Pneumadyne
- Pneumatic Valve
- ROBO Cylinder
- UR5
- actuators
- compressed air
- custom solution
- mobile industrial robot
- packaging
- stainless steel conveyors
- vision
- Belt Conveyors
- Benefits
- Bimba IntelliSense®
- CT Effects
- PLC+HMI
- Proportion Air
- Proportional valve
- Questions
- Success
- UR10
- Vaccon
- automated inspection
- food safety and sanitation
- gripper
- improvement
- industrial vision
- intelligent actuator
- life science
- pneumatic motion control
- quality assurance
- sales process
- sensor
- thomas
- valve
- 3200 series
- 6-axis robot
- 80/20
- Acro
- Belts
- Food
- LMI
- Machine
- OnRobot
- Original Line Cylinder
- Pinch Valve
- Precision Technology
- Predictive Maintenance
- Preventive Maintenance
- Product News
- ROBO Cylinders
- automated mobile robot
- autonomous mobile robot
- connectors
- controls
- covid
- custom solutions
- customer service
- e-Series
- electric actuator
- electro-mechanical
- end of arm tools
- energy plant
- ethercat
- external resource
- flexmove technology
- guarding
- labeling application
- machine control
- manufacturers
- medical
- medical industry
- monitoring
- motion
- new product
- outsource
- outsourcing
- pneumatic actuator
- pneumatic valves
- precision move
- quick response solution
- regulator
- robotics solutions
- safety
- sales tools
- steel frame
- vacuum
- vacuum technology
- welded steel frame
- 7X Series Conveyor
- AMR
- Advantages
- Application
- Applied Motion Products
- Asycube 530
- Asyfeed Pocket
- Automate
- Balanced Valves
- Beverage
- CNC program
- Continuity Inspection Tool
- Control Panel
- Controllers
- Crowned Pulley
- F22 Series
- Filtration
- Fire Fighting
- Flexible Feed
- Freeze protection
- Gas
- High Pressure Regulator
- IP65
- Inspekto
- IntelliPress
- Intellisense
- International Manufacturing Technology Show 2016
- LARGO A5
- Legos
- MIRAI
- Machine Controllers
- Machine Vision
- Micropsi
- NJ
- NY
- New
- New Scale Robotics
- OEE
- Oil
- Optimization
- PACK EXPO
- PC10
- Parison Blow Molding
- Pick-it
- ProControl Series
- ROEQ
- Rain Test
- Reducing Costs
- Resin Block
- Rio Olympics
- SCHUNK
- Sanitation
- Sensors
- Smart Manufacturing
- Spot Welding
- TRD
- Temperature Controller
- Training
- Trio Manufacturing Technology
- Twist Clamp
- UR3
- UniStream
- Universal
- V-guide
- Valve Assemble
- Vane-Buster
- Versagrip
- Versagrip solenoid pinch valves
- Victory Actuator
- Vision430
- XTR Series
- Yamaha
- automated palletizing
- balanced solenoid valve series
- bimba electric
- bottle filling
- brewery
- brushless motor
- buna
- center point
- chicane
- cloud
- cobot compliance
- collaborative operation
- compact series
- composite cylinder
- conference
- cost
- date code
- demonstration
- desiccant drier
- design
- diaphragm actuator
- diaphragm-poppet valve
- direct acting valve
- dispenser
- eGuide
Get the latest in your inbox.
This post is brought you by Dorner.
A customer recently needed a system to move various sized cartons through two inkjet printers. During this process, the carton needed to be justified and then transferred 90 degrees.
To accomplish this Dorner provided them with a 6 conveyor system which included three 3200 Series Conveyors with Intralox’s patented Activated Roller Belt™ (ARB™) technology, one of Intralox’s DARB™ conveyors and two 2200 Series flat belt conveyors. With up to 8 different sizes of cartons moving through the system, the customer needed conveyors that could handle various sized without the need for changeover.
Cartons will enter onto the Intralox DARB conveyor with the short edge leading from an upstream carton taper. If the carton has not been taped properly, the reject system will activate and the DARB unit will perform a 90° transfer, moving the box down a curved skate wheel conveyor.
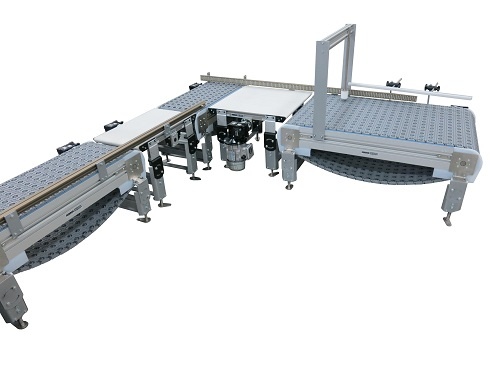
If the carton has been sealed properly, it will continue onto a 3200 Series conveyor with ARB technology. This conveyor uses Series 400 30° Chain and Activated Rollers to justify the carton against the edge where the printer is located.
After justification, the box is transferred onto a 2200 Series conveyor to allow for smooth labeling on the side of each carton with the inkjet printer. The 2200 Series conveyors are used because the rollers on the ARB conveyors would not provide a smooth enough surface.
Next, the carton travels to a 3200 Series conveyor with ARB technology using Series 400 45° Chain and Passive Rollers. This conveyor, along with the end roller guide, provides a 90° transfer onto a second Dorner 2200 Series conveyor.
Here, another ink jet printer prints information on the end of the carton. Finally, the cartons are transferred onto a 3200 Series with ARB technology conveyor which utilizes a bump turn to reorient the carton direction back to leading edge.
Interested in a Dorner Conveyor?
Interested in Learning More?
Please fill out our contact form, and a member of the Knotts Team will get in touch to help you.