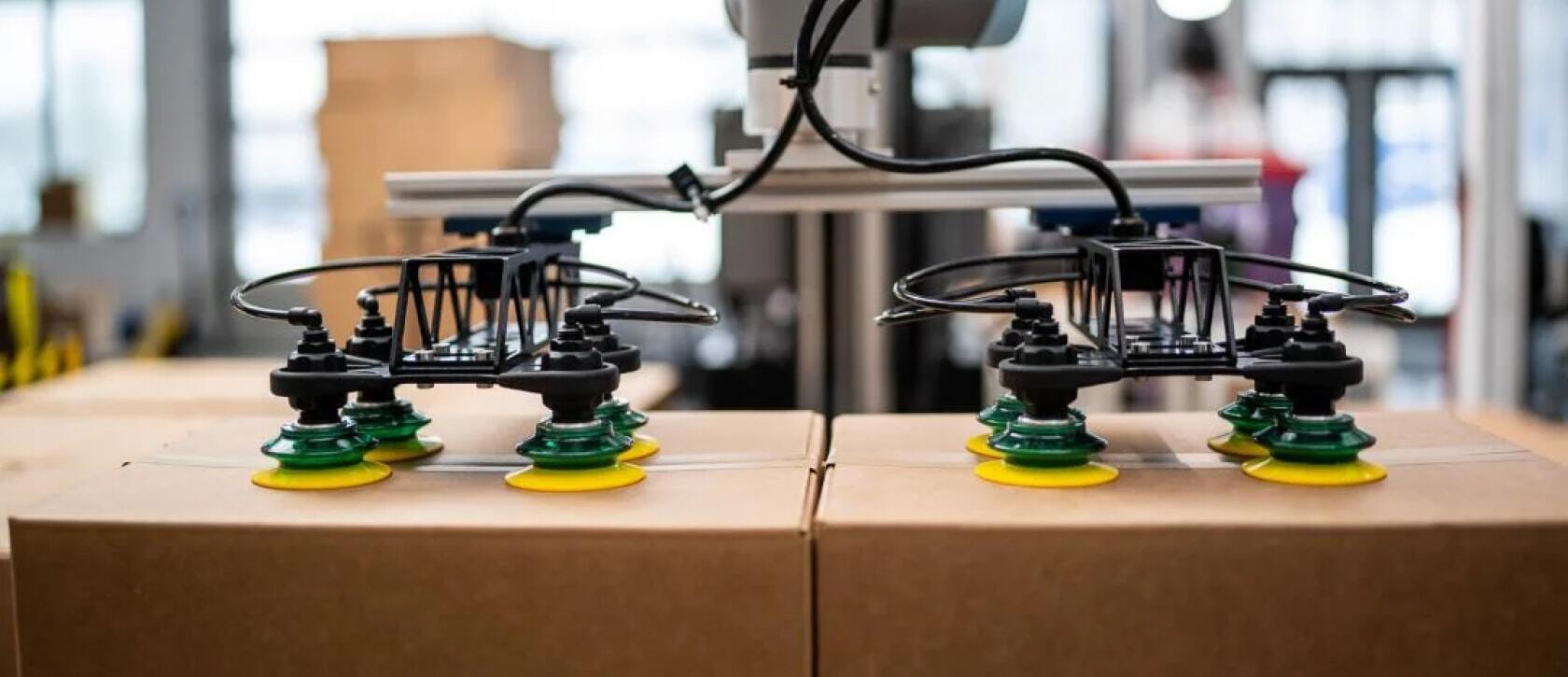
Industrial Automation & Motion Control Blog
Subscribe via Email
Subscribe to our blog to get insights sent directly to your inbox.
-
- All
- bimba
- Universal Robots
- dorner
- cobots
- industrial automation nj/ny
- Dorner Conveyors,
- The Knotts Co
- The Knotts Company
- UR
- manufacturing
- Robots
- PLC
- Unitronics
- automation
- humphrey products
- knotts company
- solutions
- HMI
- conveyors
- robotics
- aluminum extrusion
- aluminum extrusion in nj
- automation solutions
- engineered solutions
- air cylinder
- cost effective
- cost savings
- cobot
- collaborative robots
- t-slotted extrusion
- bimba solutions
- technology
- MiR
- Robotiq
- Humphrey
- IAI
- WAGO
- bimba pneumatic
- machine guard
- smartflex conveyors
- solution
- assembly
- cylinder
- electric cylinder
- motion control
- sanitary conveyor
- 2200 Series
- Products
- automation control
- collaborative robot
- conveyor
- core competencies
- grippers
- pharmaceuticals
- resource
- robot
- AquaPruf
- Asycube
- Asyril
- Cage Clamp
- Machine Guarding
- Mobile Robots
- Norgren
- OptoForce
- Pneumadyne
- Pneumatic Valve
- ROBO Cylinder
- UR5
- actuators
- compressed air
- custom solution
- mobile industrial robot
- packaging
- stainless steel conveyors
- vision
- Belt Conveyors
- Benefits
- Bimba IntelliSense®
- CT Effects
- PLC+HMI
- Proportion Air
- Proportional valve
- Questions
- Success
- UR10
- Vaccon
- automated inspection
- food safety and sanitation
- gripper
- improvement
- industrial vision
- intelligent actuator
- life science
- pneumatic motion control
- quality assurance
- sales process
- sensor
- thomas
- valve
- 3200 series
- 6-axis robot
- 80/20
- Acro
- Belts
- Food
- LMI
- Machine
- OnRobot
- Original Line Cylinder
- Pinch Valve
- Precision Technology
- Predictive Maintenance
- Preventive Maintenance
- Product News
- ROBO Cylinders
- automated mobile robot
- autonomous mobile robot
- connectors
- controls
- covid
- custom solutions
- customer service
- e-Series
- electric actuator
- electro-mechanical
- end of arm tools
- energy plant
- ethercat
- external resource
- flexmove technology
- guarding
- labeling application
- machine control
- manufacturers
- medical
- medical industry
- monitoring
- motion
- new product
- outsource
- outsourcing
- pneumatic actuator
- pneumatic valves
- precision move
- quick response solution
- regulator
- robotics solutions
- safety
- sales tools
- steel frame
- vacuum
- vacuum technology
- welded steel frame
- 7X Series Conveyor
- AMR
- Advantages
- Application
- Applied Motion Products
- Asycube 530
- Asyfeed Pocket
- Automate
- Balanced Valves
- Beverage
- CNC program
- Continuity Inspection Tool
- Control Panel
- Controllers
- Crowned Pulley
- F22 Series
- Filtration
- Fire Fighting
- Flexible Feed
- Freeze protection
- Gas
- High Pressure Regulator
- IP65
- Inspekto
- IntelliPress
- Intellisense
- International Manufacturing Technology Show 2016
- LARGO A5
- Legos
- MIRAI
- Machine Controllers
- Machine Vision
- Micropsi
- NJ
- NY
- New
- New Scale Robotics
- OEE
- Oil
- Optimization
- PACK EXPO
- PC10
- Parison Blow Molding
- Pick-it
- ProControl Series
- ROEQ
- Rain Test
- Reducing Costs
- Resin Block
- Rio Olympics
- SCHUNK
- Sanitation
- Sensors
- Smart Manufacturing
- Spot Welding
- TRD
- Temperature Controller
- Training
- Trio Manufacturing Technology
- Twist Clamp
- UR3
- UniStream
- Universal
- V-guide
- Valve Assemble
- Vane-Buster
- Versagrip
- Versagrip solenoid pinch valves
- Victory Actuator
- Vision430
- XTR Series
- Yamaha
- balanced solenoid valve series
- bimba electric
- bottle filling
- brewery
- brushless motor
- buna
- center point
- chicane
- cloud
- cobot compliance
- collaborative operation
- compact series
- composite cylinder
- conference
- cost
- date code
- demonstration
- desiccant drier
- design
- diaphragm actuator
- diaphragm-poppet valve
- direct acting valve
- dispenser
- eGuide
- elastomers